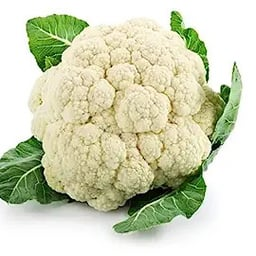

Free software (not open-source, it’s really free software that’s important) that depends on a single for-profit vendor is not free.
MicroG is open-source but it’s not free. It fails to address two problems:
- What do I care looking at the source code of a Google Play Services replacement when Google still holds my cellphone by the balls for certain critical functions?
- Why do I need permission from Google for apps to function properly on my cellphone?
I don’t think OP cares about getting the source of the apps they run so much as the apps being free-as-in-libre in his original question. Many people mistake open-source for free software and MicroG is not truly free.
Funny you should ask: I installed Debian 32-bit on an old Asus Eee PC netbook yesterday to breathe new life into that old machine and turn it into a controller for a piece of test equipment we have at work. My company keeps old stuff like that around until space is needed in case someone needs something.
Just in case I had to modify something in the tester’s control software, I figured I’d install i3wm and Vim. It didn’t take long and I was surprised by how usable the machine ended up being. Honestly I wouldn’t have minded using it as a bone fide laptop for light-duty work on the go.
So basically keep your expectations low and install super-lightweight software, and your old Aspire could live a few extra productive years instead of going to the landfill.